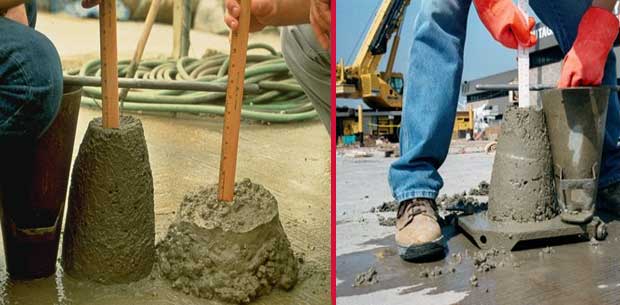
Workability of concrete is defined as the ease and homogeneity with which a freshly mixed concrete or mortar can be mixed, placed, compacted and finished. Strictly, it is the amount of useful internal work necessary to produce 100% compaction.
Another similar term used to describe a freshly prepared concrete is ‘consistency’ which is the ease with which it will flow. It is the wetness of the concrete and the measure of fluidity or mobility. Wet concretes are more workable than dry concrete, but concretes of the same consistency may vary in workability. A concrete which has high consistency and which is more mobile, need not be of right workability for a particular job. Type of work, thickness of section, reinforcements and mode of compaction are the aspects to be considered while specifying the workability for any particular job.
Contents:
Factors affecting workability
Workable concrete shows very less internal friction between particles and overcomes the frictional resistance with just the amount of compacting efforts provided. Workability of the concrete depends on a number of interrelating factors. Water content, aggregate properties, use of admixtures, fineness of cement are the factors affecting workability.
- Water content: The increase in water content increases the fluidity of the concrete thus providing greater lubrication. This helps to increase the workability of the concrete. Increasing the water content should be the last resort to improve the workability in the concrete as this will seriously affect the strength of the concrete. Even if more amount of water is to be added, more cement also should be added so that the water/ cement ratio remains the same and hence the strength of the concrete remains unaffected.
- Size of aggregates: The surface area of bigger aggregates is less and hence less amount of water is required for lubricating the surface to reduce the friction. Thus the concrete having large sized aggregate is more workable (of course, within certain limits).
- Mix proportions: Aggregate/ cement ratio is the measure of how lean or rich the concrete is. If aggregate/ cement ratio is higher, the concrete becomes leaner. In lean concrete less paste is available for the lubrication of the aggregate, while in rich concrete with low a/c ratio, more paste is available which makes the mix more cohesive and hence provides better workability.
- Shape of aggregates: Rounded aggregates have considerably less surface area and less voids in comparison to angular or flaky aggregates which provide better possibility of overcoming the frictional resistance. Further, angular and flaky aggregates make concrete very harsh.
- Surface texture of aggregates: The aggregates having smooth or glossy texture have less surface area compared to rough textured aggregates. This provides better workability as less amount of water is required for lubricating effect. But, taking into account the poor interlocking action provided by the glossy textured aggregate, its use is generally discouraged in high strength concrete.
- Grading of aggregates: Well graded aggregate is the one with least amount of voids in a given volume. If the grading of aggregate is good, the voids will be less and hence higher the workability.
- Use of admixtures: Use of admixtures in concrete is the major factor that affects the workability. The use of plasticizers and super-plasticizers amply increase the workability of the concrete. Air entraining agents produce air bubbles which act as rollers between particles and provide better mobility thus improving the workability.
- Time and temperature: Fresh concrete gets stiffened as the time flows. This is because some of the water used to mix the concrete gets evaporated and some gets absorbed by the aggregates. Thus the workability of concrete reduces with time. This loss of workability with time is known as slump loss. The effect of temperature on workability of concrete is noteworthy. As the temperature increases, the workability of the mix reduces.
Measurements of workability/Workability Tests
Slump test
It is the most common method for measuring the workability of freshly mixed concrete. It can be performed both in lab and at site. Uniformity of the concrete regarding workability and quality aspects can be assessed from batch to batch by observing the nature in which the concrete slumps. It is not very suitable for very wet or very dry concrete.
A steel mould in the form of frustum of cone is used in slump test which has the top diameter of 100 mm, bottom diameter of 200 mm and the height is 300 mm. According to Indian standard specification, the maximum size of the aggregate in concrete that can be used to perform slump test is restricted to 38 mm.
The mould is cleaned and freed from any surface moistures and then the concrete is placed in three layers. Each layer is tamped 25 times with a standard tamping rod (16 mm dia, 0.6 meter length). Immediately after filling, the cone is slowly lifted and the concrete is allowed to subside. The decrease in the height of the center of the slumped concrete is called slump and is measured to the nearest 5mm.
If the concrete subsides evenly all round, the slump measured is true slump. If one half of the cone slides down an inclined plane, a shear slump is said to have taken place and the test has to be repeated. Too wet mix shows collapsible nature of slump.
Compacting factor test
This test is generally carried out in laboratory but can be used in site also. It is particularly useful for concrete mixes of very low workability (or very dry concrete) as they are insensitive to slump test.
This test works on the principle of determining the degree of compaction achieved by a standard amount of work done by allowing the concrete to fall through a standard height.
Container | Top diameter (mm) | Bottom diameter (mm) | Height (mm) |
Upper hopper | 254 | 127 | 279 |
Lower hopper | 229 | 127 | 229 |
Cylinder | 152 | 152 | 305 |
Distance between bottom of upper hopper and top of lower hopper = 203 mm | |||
Distance between bottom of lower hopper and top of cylinder = 203 mm |
The concrete is placed in the upper hopper gently so that no effort is applied to produce compaction. The bottom door is opened so that the concrete falls on the lower hopper. Again the bottom door of the lower hopper is opened and the concrete falls on the cylinder. After removing the excess concrete by the help of blades, the weight of the cylinder (known volume) is taken to nearest 10 grams. This weight is known as “weight of partially compacted concrete”. The cylinder is emptied and then filled with the same sample rammed heavily so as to obtain full compaction. The cylinder is weighed to nearest 10 grams. This weight is known as “weight of fully compacted concrete”.
Compacting factor = (weight of partially compacted concrete) / (weight of fully compacted concrete)
Vee-Bee test
Vee-Bee test is a good laboratory test suitable for stiff concrete mixes having low and very low workability. It consists of a vibrating table, a metal pot, a sheet of metal cone and a standard iron rod.
In this test, Slump test as mentioned above is performed by placing the slump cone inside the sheet metal cylindrical pot. Then the vibration is started and the time on a stop watch is noted. The time taken by the concrete to take cylindrical shape after the conical shape disappears is noted. This time recorded is known as Vee-Bee Degree or Vee-Bee seconds.
Workability of concrete (comparison of Slump test, Compacting Factor Test and Vee-Bee Test) | ||||
Degree of workability | Slump (mm) | Compacting factor | Vee-Bee Test
(seconds) |
Suitability |
Very low | 0 – 25 | 0.78 | 20 – 10 | · Roads where mechanical vibrators are used. |
Low | 25 – 50 | 0.85 | 10 – 5 | · Roads where compaction is done manually.
· Mass concrete foundations without vibration. · Lightly reinforced sections with vibration. |
Medium | 25 – 100 | 0.92 | 5 – 2 | · Manually compacted flat slabs.
· Manually compacted normal reinforced concrete. · Heavily reinforced sections with vibration. |
High | 100 – 175 | 0.95 | 2 – 0 | · Sections with congested reinforcement without vibration. |
Flow Test
This is a laboratory test. It gives an indication of the quality of the concrete with respect to consistency, cohesiveness and the proneness to segregation. The spread of the flow of the concrete is measured and this is related to workability. This test is best suitable for flowing concrete made by the use of superplasticizing admixtures.
Kelly Ball Test
This is a simple field test consisting of the determination of the indentation made by 15 cm diameter metal hemisphere weighing 13.6 kg when freely placed on fresh concrete. It is quite faster and provides precise measurement of workability than slump test. But it requires large amount of concrete to be performed.