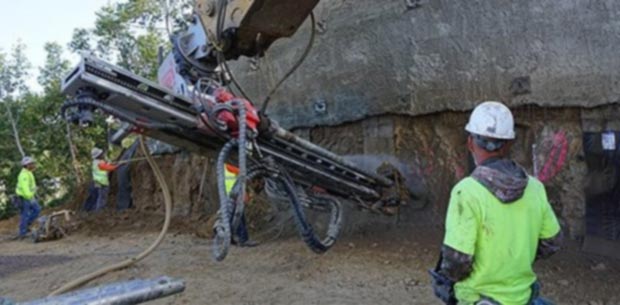
Drilling, also known as boring, is easily done by employing specialized equipment called rock drills. The most commonly used types of drills are:
- The hydraulic drills
- Electric motor drills
- Pneumatic rock drills
These three include some of the most important tools in a variety of projects such as soil nailing, micro-pile, mining and tunneling job sites. Industry professionals prefer hydraulic drills because of their specific advantages over the other types of drills. Some of these benefits include their light weight and ability to operate on hard rocks without using a large compressor.
Parts of a Rock Drill
Regardless of the industry, all types of rock drills have a standard design that is essentially a combination of replaceable attachments. The most significant parts of a standard rock drill include the following:
- Drill bit: This is the tip of the rock drill that first makes contact with the ground during a boring operation.
- Drill stem: This is the long frame that penetrates the ground during boring whose end houses the drill bit.
- Drill rod: This is the hollow part of the drill stem that connects the motor of the rig to the drill bit. The drill rod is also responsible for transferring the cutting force to the drill bit to enable the rock drill to penetrate into the ground.
- Carbide bits: These are special types of drill bits used in rotary and percussive drilling that have carbide tungsten coated onto them at an angle.
How Rock Drills Work
During soil nailing, micropile, mining or tunneling operations, rock drills penetrate the earth either by rotating or creating continuous impact blows. Rotary drills are the most common and operate by cutting and flushing out rock fragments, while percussive drilling breaks rocks by creating impact blows. Some contractors choose to combine both methods which are quite effective for operations on medium to hard rocks.
The method of drilling also depends on the type of hole a contractor intends to bore into the ground. The two commonly preferred holes are the cored holes and the open holes. Cored holes have an opening whose diameter is predetermined before an operation. In this case, cored holes require a stem with outer tubes to rotate the drill bit.
On the other hand, open holes have no predetermined diameter. The drill bit penetrates straight into the ground during an operation. There are three main types of drill bits that are employed in boring open holes. These include rock roller bits, wing bits and down-the-hole hammers.
Rock roller bits, also known as tricone bits, have teeth-like steel cones. These cones cut and flush rock fragments outwards through the drill rod. Wing bits, also known as drag bits, are made of carbide tungsten and are suitable for soft ground surfaces. Air core hammers have three protruding blades that cut rock during an operation and use compressed air to flush out fragments on the surface.
For more information, or to know about quality products offered on rock drills, please visit TEI Rock Drills.